使用顺酐时要防止烟火、高温、日晒、潮湿、猛烈撞击、与皮肤接触。远离火源、氧化剂、食品。下面
氢氧化钾厂家来讲讲两种氧化制顺酐的反应表现。
When using maleic anhydride, it is necessary to prevent fireworks, high temperature, sunlight, humidity, violent impact and contact with skin. Keep away from fire, oxidant and food. The following potassium hydroxide manufacturer will talk about the reaction performance of two oxidation to maleic anhydride.
苯氧化制顺酐的反应
Reaction of Benzene Oxidation to Maleic Anhydride
将苯与空气混合(苯为1%-1.4%)经换热器预热后,进人列管式催化反应器。在压力为0.1-0.2MPa、温度为350-400℃的反应条件下进行氧化反应,所得产物经两台换热器、一台冷却器后,冷却到接近露点(55―65℃)。冷却后的反应物进入分离器,分离器底部得粗顺酐,进入粗顺酐罐。
The benzene is mixed with air (benzene is 1% - 1.4%), preheated by the heat exchanger, and then enters the tubular catalytic reactor. The oxidation reaction is carried out under the reaction conditions of 0.1-0.2MPa pressure and 350-400 ℃ temperature. The product is cooled to close to the dew point (55-65 ℃) after passing through two heat exchangers and one cooler. The cooled reactants enter the separator, and the crude maleic anhydride obtained at the bottom of the separator enters the crude maleic anhydride tank.
分离器顶部流出物进人洗涤塔,用水洗涤,塔顶为多余空气和未反应的苯,苯可用吸附回收。洗涤塔塔底水溶液进人脱水器,分离出水,所得粗顺酐进人粗顺酐罐。粗顺酐进一步进人蒸馏塔进行蒸馏精制,得顺酐。所得顺酐可进行异构化得富马酸和苹果酸。
The effluent from the top of the separator enters the scrubber and is washed with water. The top of the scrubber contains excess air and unreacted benzene, which can be recovered by adsorption. The water solution at the bottom of the scrubber enters the dehydrator, the effluent is separated, and the obtained crude maleic anhydride enters the crude maleic anhydride tank. The crude maleic anhydride is further fed into the distillation tower for distillation and refining to obtain maleic anhydride. The obtained maleic anhydride can be isomerized to obtain fumaric acid and malic acid.
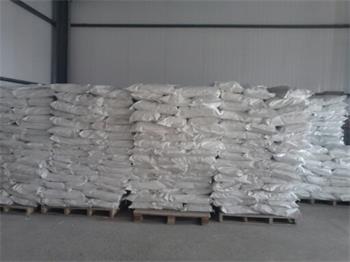
C4馏分部分氧化制顺酐的反应
Partial Oxidation of C4 Fraction to Maleic Anhydride
工业上用不经分离的C4馏分或分离异丁烯和丁二烯后的C4馏分为原料生产顺酐。C4馏分部分氧化制顺酐的工艺流程见下图。C4馏分与空气混合后进人流化床氧化反应器,在300―500℃温度下,与反应器中的催化剂接触生产顺酐。
In industry, maleic anhydride is produced from C4 fraction without separation or C4 fraction after isobutene and butadiene separation. The process flow of partial oxidation of C4 fraction to maleic anhydride is shown in the figure below. C4 fraction is mixed with air and then enters the fluidized bed oxidation reactor. At the temperature of 300-500 ℃, it contacts with the catalyst in the reactor to produce maleic anhydride.
氧化反应器顶部流出的反应生成物进人吸收塔,用水作为吸收剂,塔顶气体经废水处理塔后排出。吸收塔塔底水溶液进人脱水塔,进行浓缩脱水,后进入精制塔经简单蒸馏,得顺酐产品。
The reaction products from the top of the oxidation reactor enter the absorption tower, and water is used as the absorbent. The gas from the tower top is discharged after passing through the wastewater treatment tower. The water solution at the bottom of the absorption tower enters the dehydration tower for concentration and dehydration, and then enters the refining tower for simple distillation to obtain maleic anhydride.
与苯氧化制顺酐相比,C4馏分部分氧化制顺酐具有原料成本低、催化剂寿命长等优点,但是,顺酐的选择性低,且投资费用大。
Compared with the oxidation of benzene to maleic anhydride, the partial oxidation of C4 fraction to maleic anhydride has the advantages of low raw material cost and long catalyst life. However, the selectivity of maleic anhydride is low and the investment cost is large.
In addition, the packaging of maleic anhydride products should be sealed, with obvious signs of "corrosive articles". Personal safety should be the priority. More relevant matters can be found on our website http://www.jinhao360.com consulting service